Revolutionizing EV Charging Through Transformative Design
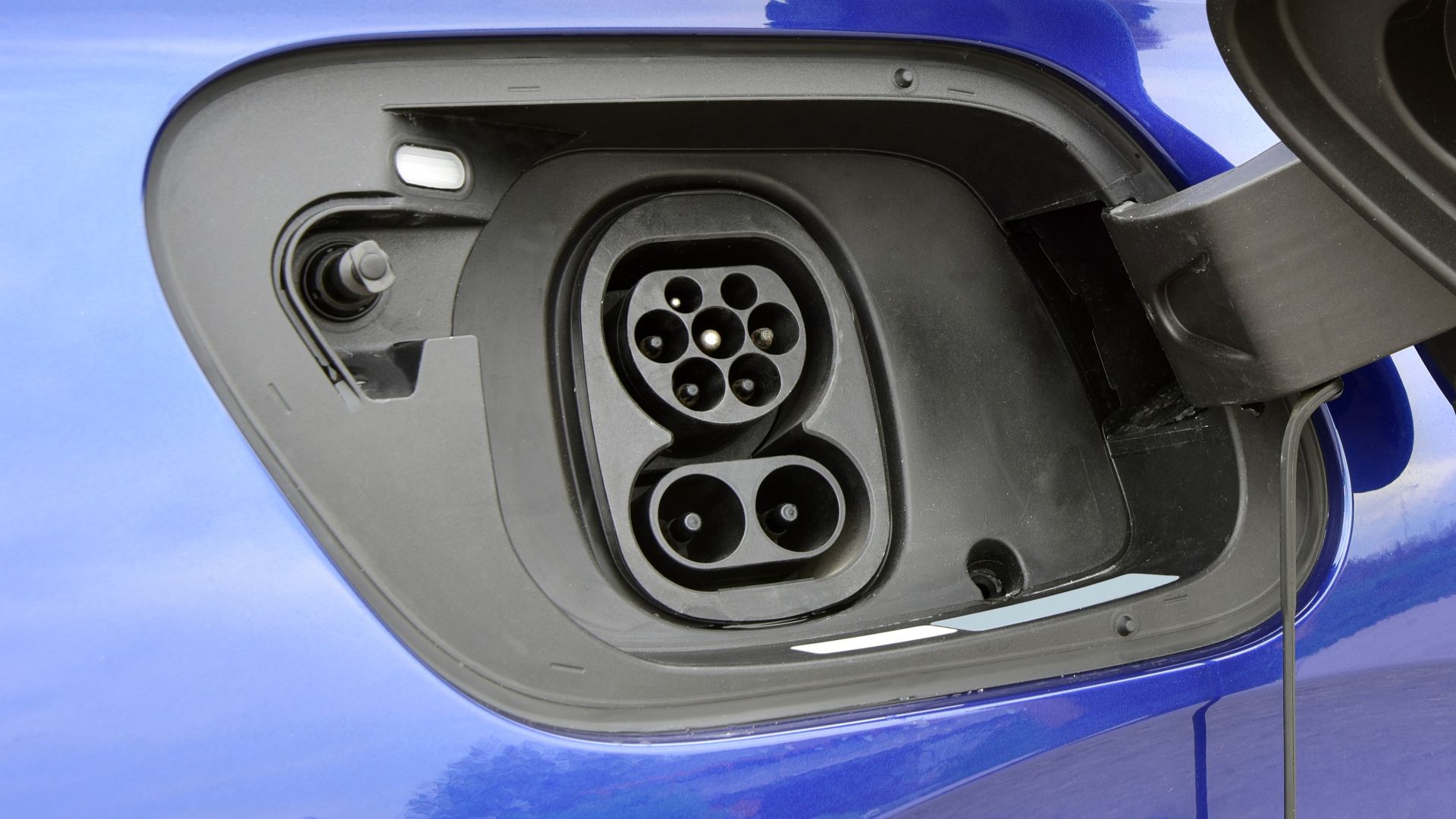
*illustrative picture only
Ease of charging is a key factor influencing electric vehicle adoption, however the limitations of conventional cable designs are hindering the effort to increase charging speed. Voltaira Autokabel’s busbar DC charger utilizes a pioneering conductor technology to advance the fast charging experience for customers.
The cable connection between the battery and the charging inlet of an electric vehicle plays a crucial role in determining charging speed. Fast charging requires currents of up to 1kA, which in turn demands the increase of conductor cross-section to prevent power loss and overheating. However, this approach is reaching its limits as cable chargers weighing up to 4kg could be needed, lowering efficiency, with bulky designs making integration into vehicles challenging.
The aluminum busbar technology pioneered by Voltaira Autokabel in 2004 offers numerous advantages over copper cables, making it well-suited for demanding high-voltage applications, including fast charging of electric vehicle batteries.
Higher currents, less weight
The improved heat dissipation coming from the rectangular shape of the flat busbar conductor ensures excellent thermal behavior. For instance, at a continuous charging current of 1kA RMS, a single busbar’s temperature can be reduced by 40% compared to a non-shielded copper cable with the same electrical resistance. This allows for a substantial shortening of charging time by increasing charging current without the danger of overheating.
The busbar’s low-resistance connection to the battery and the charging inlet is ensured by low-impedance screw connections and our advanced friction welding process, which eliminates contact resistance between aluminum and the copper screw bushings. In addition to aiding high current fast charging, screw connections also enable the safe and easy disconnection of the battery and the charging inlet for servicing.
The use of light-weight aluminum as the conductor material advances weight reduction. Additionally, the rigid nature of busbars makes it possible to apply a special insulation process and new insulating materials, such as polyamides for a significantly thinner insulation layer. Coupled with the lesser need for fixtures used heavily to keep flexible cables in position, it further propels weight-efficient design and the extension of electric vehicles’ driving range.
Tailored to unique needs
Voltaira Autokabel has collaborated with several international OEMs, including premium car manufacturers to integrate our award-winning DC charger solution into electric vehicles. During these projects, we successfully fulfilled strict requirements for watertightness and vibration resistance. It underlines our ability to engineer our products according to the most demanding standards, and how the highly automated manufacturing process of our busbar-based charger solution ensures superior quality.
As another advantage, the flexible design facilitates easy integration. By leveraging our capacity for deep-level customization, we tailor the charging inlet to accommodate different charging standards. The option for connecting the conductor to the charging inlet from multiple directions and angles, in addition to our ability to perfectly adapt busbars to the installation space thanks to their flat shape and semi-rigid properties, further eases integration.
Moreover, the rigidity of busbars makes cable unwinding unnecessary and handling easier at the installation phase, resulting in a streamlined and cost-optimized process for OEMs.
Cutting-edge solutions in your support
Our busbar DC charger offers car manufacturers a competitive advantage. By shortening charging times through enabling higher currents, it significantly enhances the charging experience for customers, while its low-weight design improves energy efficiency and range of electric vehicles.
The pioneering charger concept, along with Voltaira’s over 1100 automotive patents showcases our ability to deliver cutting-edge solutions. With more than 450 engineers working on new mobility solutions, we are committed to supporting our OEM customers by providing advanced power distribution, data connectivity and sensor solutions that help them to maintain a competitive edge in the rapidly transforming automotive market.
Challenges
- Strong need to improve the charging experience
- Increasing charging currents
- Cable-based charger designs are reaching their limits
- Installation space constraints
Solutions
- Aluminum busbar replaces cable as the conductor
- Low-weight thin insulation layer
- Customizable design
- Highly automated production
Results
- A pioneering concept offering product differentiation for OEMs
- Faster charging improves customer experience
- Reduced conductor weight extends EV range
- Easy disconnection of the battery and the charging inlet for servicing
- Heavily tailored designs support integration