Voltaira: The End-to-End Supplier of O2 Sensor Harnesses
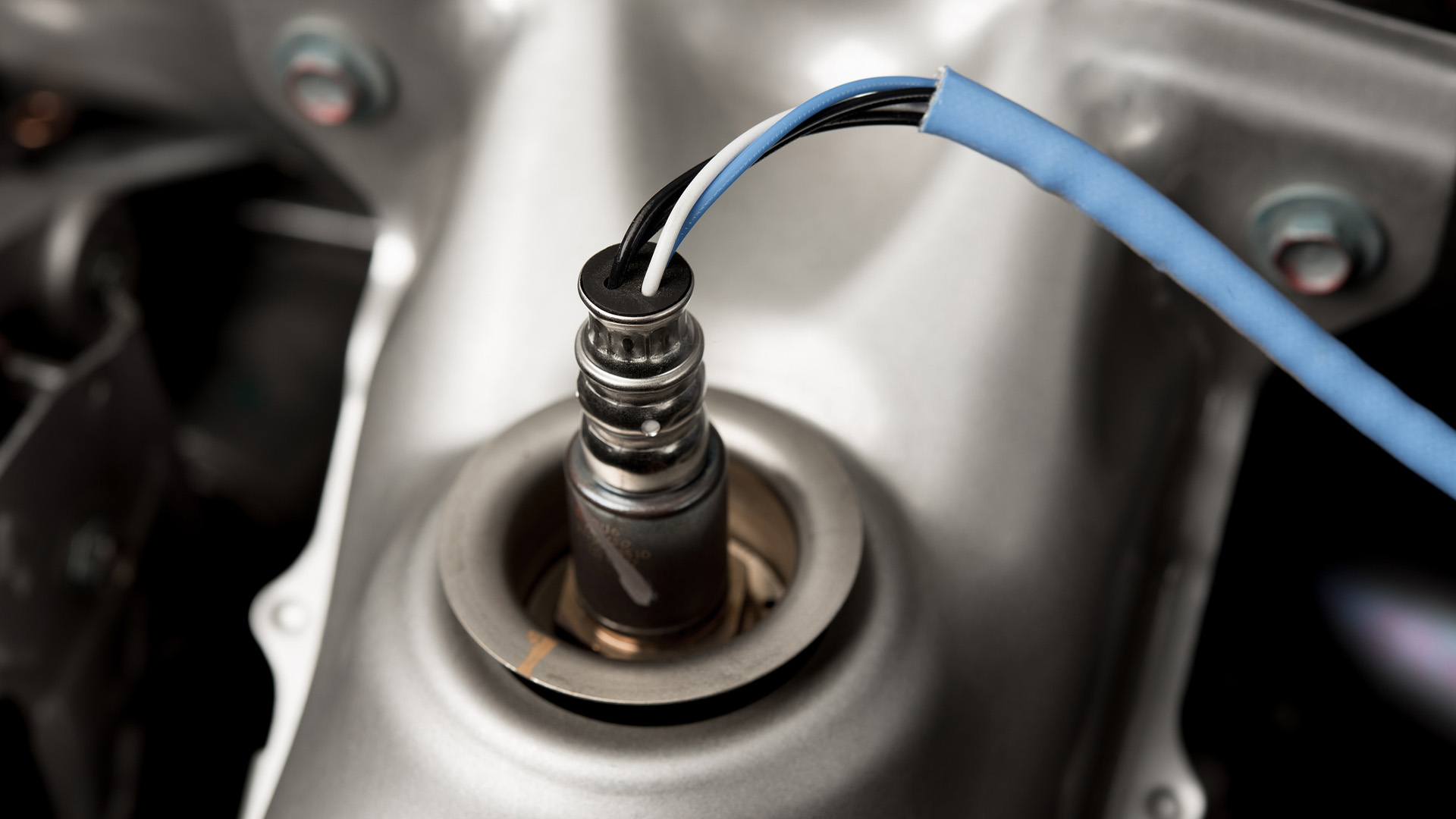
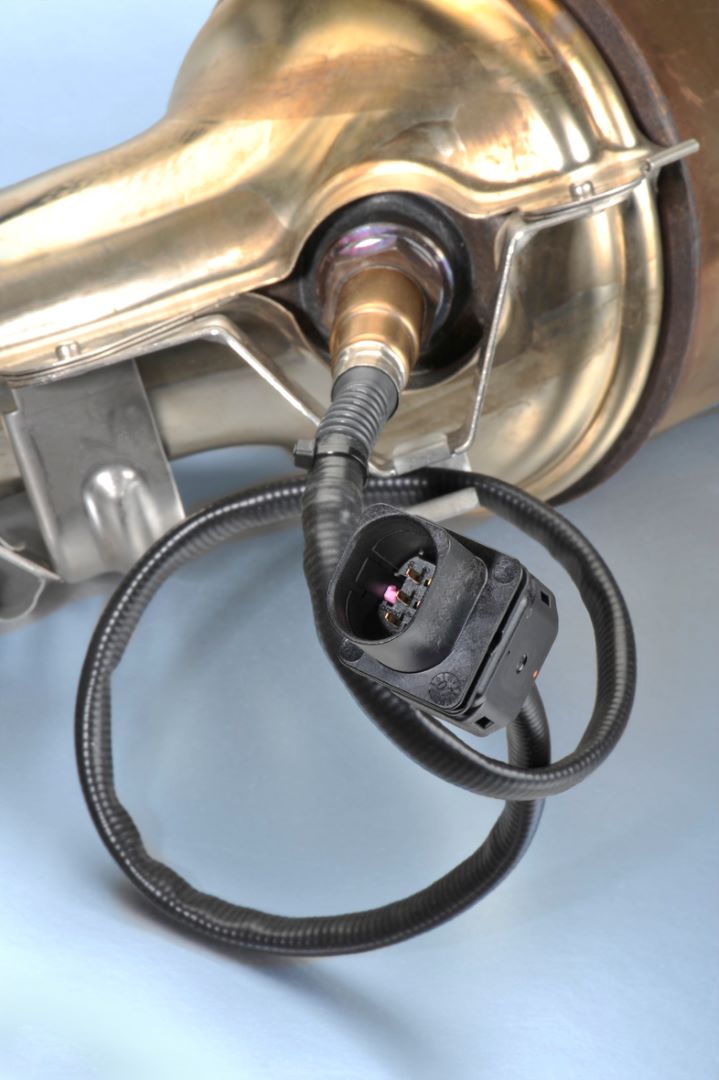
*illustrative picture only
*picture of Voltaira product
.
Cars powered fully or partly by internal combustion engines will remain on our roads in significant numbers for decades. Voltaira, with its extensive expertise in the serial production of oxygen sensor wire harnesses for the largest Tier 1 automotive suppliers, is well-positioned to support the ICE technology throughout its entire lifecycle.
By enabling the engine Electronic Control Unit (ECU) to optimize the fuel-air ratio, oxygen sensors play an important role in minimizing emissions, ensuring good fuel efficiency, and maintaining the health of the engine and the catalytic converter. However, to fulfill their function, the sensors must have a reliable connection to the engine ECU—and here is where Voltaira comes in with its more than 30 years of experience in build-to-print manufacturing of oxygen sensor wire harnesses for leading suppliers. Voltaira’s wiring harnesses have consistently proven their robustness and outstanding quality across almost all major OEMs’ models, showcasing our capabilities and commitment to excellence.
Meeting the highest quality standards
Located right outside the exhaust system, the O2 sensor harnesses must function in temperatures reaching up to 400 degrees Celsius. Waterproof properties, abrasion and chemical resistance against salt and oil are also required to withstand the harsh conditions in a vehicle. Voltaira not only understands these requirements but consistently meets and exceeds them through its exceptional manufacturing standards.
At Voltaira, semi-automated production of O2 sensor harnesses is executed in a clean environment, while damage to the wire and its insulation is avoided by the wire’s completely automated cutting and crimping. The self-developed manufacturing and testing equipment is another key lever in ensuring that high-quality standards of Tier 1 suppliers and OEMs are met, at the same time allowing Voltaira to have a complete in-house value chain in the manufacturing of O2 sensor harnesses.
Value-added services
Voltaira’s vertical integration capabilities support the assembly of O2 wiring harnesses according to our customers’ exact specifications. In addition to our validation and testing capabilities, as part of Foxconn Interconnect Technology (FIT) we also leverage the group’s comprehensive expertise in wire, terminal, clip and stamped parts production.
As a further value-added service on top of our blueprint manufacturing competencies, Voltaira provides engineering support to its customers. Collaborating with Tier 1 suppliers, our engineers offer expert input for standardization and improving manufacturability prior to the production phase. Voltaira also drives cost reduction through optimized logistics, including batch size optimization and regional production allocation, significantly shortening lead times. With a robust manufacturing capacity, producing 20-25 million O2 wiring harnesses annually across facilities in Europe, Africa, Asia and North-America, Voltaira aims to meet the global demand, reinforcing our commitment to delivering top-tier solutions.
Voltaira’s streamlined process drives faster time-to-production and sets us apart. We have a track record of manufacturing O2 sensor harnesses with more than 10,000 different connector designs, reflecting our expertise in managing the complexity of a large number of variants. Our flexible manufacturing system allows us to quickly adapt to new designs, making it possible to start production even in as little time as a few weeks after initial contact. This agility, combined with our ability to handle large-scale production efficiently, makes us a trusted partner for delivering high-quality connectivity solutions swiftly and reliably.
Full lifecycle management
Voltaira offers its customers end-to-end product lifecycle management support, from concept design to post-production. In the case of O2 sensor harnesses, in addition to serving customers during the series production of vehicles, we also have a wealth of experience in after-sales support by providing stable parts supply for 15-20 or even more years after a model’s production has ended. This makes us a trusted long-term partner of our customers.
Challenges
- Demand for reliability in harsh conditions
- 10,000+ connector designs to work with
- Minimized wire damage through advanced technologies
- Need for end-to-end product lifecycle support
Solutions
- Semi-automated production for quality and consistency
- Wide-range of value-added services from engineering support to validation and testing
- Mass production services
- End-to-end product lifecycle management support
Results
- Trusted partner of Tier 1s for over 30 years
- 20-25 million high quality parts produced per year
- Significant cost savings over partnership lifetimes
- Stable parts supply during the product lifecycle