Lighter, Stronger, Better: Reinventing Electrical Connectivity
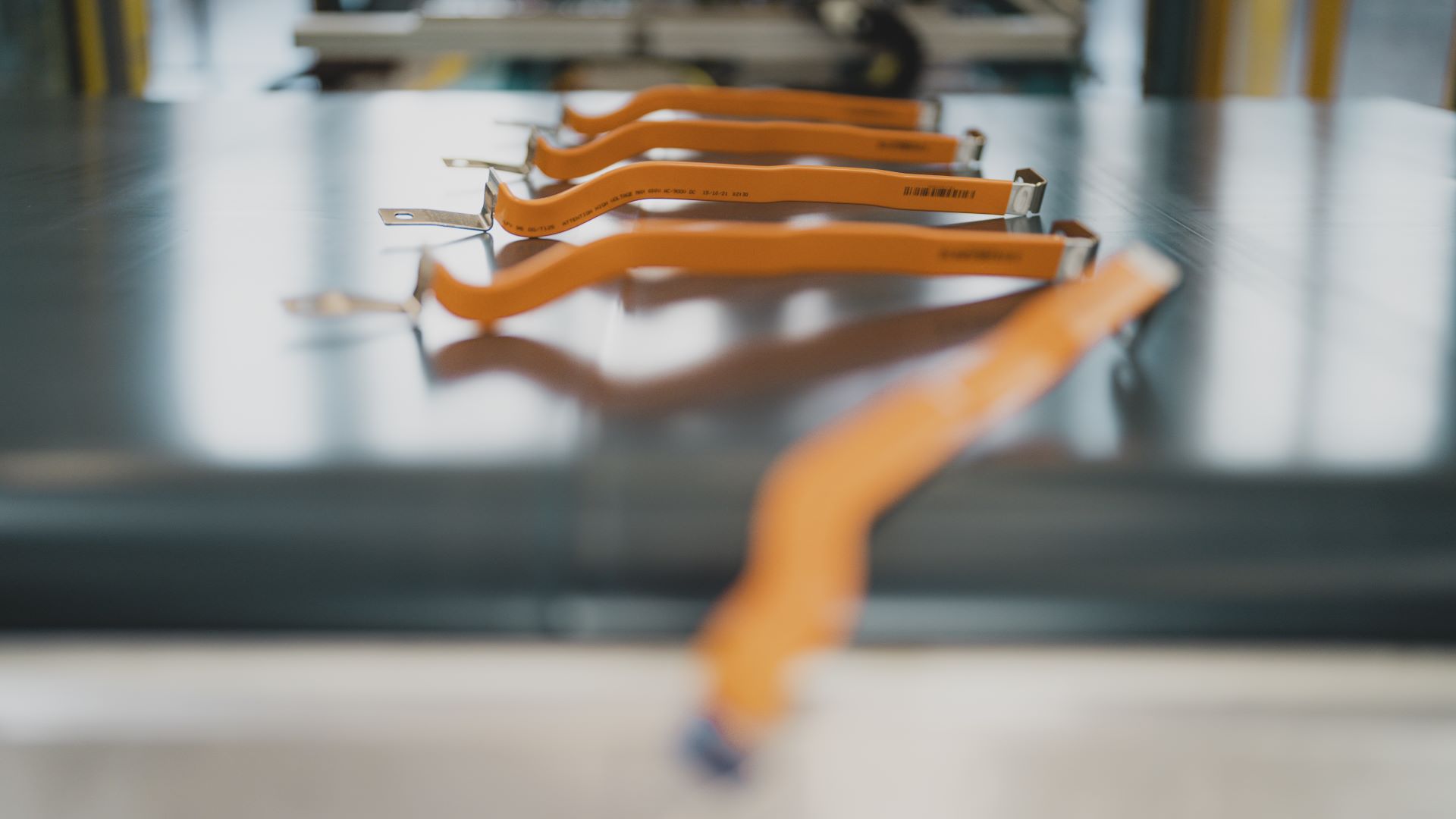
*picture of Voltaira product
Cable harnesses are an essential component of vehicles, however there is an increasing need to rethink the wiring system of automobiles as the number of electrical components grows and electrification progresses. The aluminum busbar technology pioneered by Voltaira Autokabel offers weight reduction and an ideal solution for modern high-voltage applications.
In traditional wiring harnesses, clips and channels keep the flexible cable in position throughout the vehicle’s lifetime. In 2004, Voltaira Autokabel’s engineers envisioned an innovative rigid solution that mitigates the use of fixtures and allows for weight reduction while maintaining production cost levels. As a result, by 2007, the first aluminum busbar in the automotive industry was put into series production for a global premium car manufacturer.
Ready for electrification
The substantial 40% weight saving compared to copper cables with the same electrical resistance is one of the numerous benefits that established the aluminum-based technology as the preferred choice for a multitude of OEMs. The elimination of forming and retaining elements, combined with the thin insulation achieved by new materials and a special insulation process propel further weight reduction.
Busbars also support efficient space utilization—another important requirement as wiring systems grow. The rigid flat-shaped conductors adapt perfectly to the installation space, while the need to increase cross-section because of the lower conductivity of aluminum is partly compensated by the intermetallic connection technologies eliminating contact resistance and the improved heat emittance made possible by the larger surface area. The improved thermal behavior also gives aluminum busbars significantly larger current carrying capacity when compared to copper cables with similar resistance, making them perfectly suited for demanding high-voltage applications.
Manufacturing excellence
The flexibility of Voltaira’s production system supports the cost-efficient fulfillment of OEMs’ requirements. Depending on design and series size, busbar production using CO2-reduced aluminum is conducted on manual, semi, or fully automated manufacturing lines, utilizing in-house developed bending technology. The wide range of connection solutions including ultrasonic, friction, resistance and laser welding increases design flexibility, while sophisticated 3D visual measurement techniques ensure the maintenance of tight tolerances.
We manufacture our busbar solutions in Europe, China, and Mexico, allowing us to localize production close to our customers. In addition to the optimization of logistical costs offered by our global footprint, customers also enjoy a simplified and quicker installation process coming from the rigid nature of busbars which makes handling easier and cable unwinding unnecessary, advancing cost reduction in the vehicle assembly process.
Innovating in co-operation
Voltaira’s strong co-development capabilities, also underscored by our more than 60 strategic development partners, allow us to co-operate with car manufacturers from the early phase of new model development to ensure seamless integration of busbars.
We offer customized power transmission, data connectivity and sensor solutions for a wide range of needs. In case of busbars, our wealth of experience with 12V busbar applications support us in adapting the technology to the high-voltage systems of electric vehicles, while our varied material and connection technologies further advance design flexibility.
The more than a dozen automobile brands, among them premium and sports car manufacturers, which placed their trust in our busbar products is a testament to the versatility and reliability of the cutting-edge technology. With over 1100 automotive patents, and with more than 450 engineers dedicated to the mobility of tomorrow, Voltaira is well-positioned to continue offering innovative solutions to leading global OEMs as the automotive industry continues to transform.
Challenges
- Wiring systems are growing in size and weight
- Flexible harnesses require the use of fixtures
- Time-intensive manual harness installation processes
Solutions
- Low-weight aluminum-based technology
- Manual, semi, or fully automated manufacturing lines
- Advanced connection solutions
- Sophisticated 3D visual measurement techniques
Results
- Pioneering technology
- Supports next-generation body harness architectures
- 40% weight saving compared to copper cables
- Optimized vehicle assembly process – simple & quick
- Efficient space utilization